First: the appearance of steel pipe inspection (1) before the anti-corrosion, the appearance of steel pipe should be visually observed by skilled workers root by root, the steel pipe with or without serious mechanical damage, heavy skin, cracks, depressions and other defects, inspection of unqualified steel pipe can not be used, and make a failure to mark the return. Acceptance of qualified before being used for construction. (2) Pipe mouth if there is a flat mouth situation, should be timely rounding repair, can not be repaired should be scrapped.
Second: Descaling of working steel pipe (1) Firstly, the steel pipe to be anticorrosive will be transported to the upper pipe platform of the working line with the pipe grabber, and the flame heater device will be used to preheat the outer surface of the steel pipe to drive away the moisture, oil and impurities on the surface of the steel pipe, and the heating temperature will be controlled at 40℃~60℃ to improve the quality of descaling of the surface of the steel pipe. (2) Steel pipes are descaled by PW-380 steel pipe shot blasting and descaling machine, after the steel pipe enters the shot blasting machine, the surface of the steel pipe after shot blasting and descaling should reach the Sa2.5 level stipulated in "Rust Level and Descaling Level of Steel Surface before Painting" GB/T8923-1988, and the depth of the anchor grain on the surface should be carried out in accordance with the instructions provided by the manufacturer. (3) After the surface pretreatment, all the rust, oil, oxide skin, etc. should be removed. (4) The outer surface of the steel pipe shall be inspected root by root, and the surface defects which may lead to leakage of coating points shall be polished by suitable methods, and the wall thickness after polishing shall not be less than the specified value. The steel pipe with defects shall be rejected or repaired. (5) The steel pipe with unqualified descaling quality shall be taken off the line in time to remove the throws in the pipe, and then return to the production line to descale again.
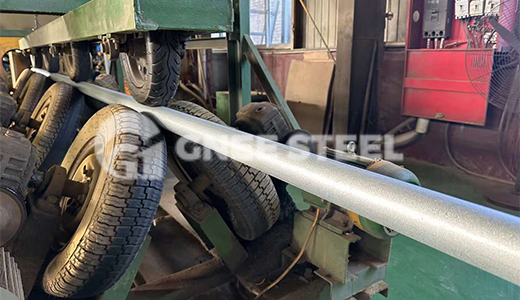
Third: steel pipe surface dust treatment (1) steel pipe by shot blasting rust removal, in the next process before the epoxy powder high-pressure electrostatic spraying, the use of dust treatment device on the external surface of the steel pipe for secondary treatment, the steel pipe surface residual rust powder dust removal, and should be within 4 hours of the epoxy powder coating, if more than 4 hours or the surface of the steel pipe appears to return to the surface of the rust must be re-treated surface pre-treatment. When the surface of steel pipe is treated with fine dust, the induced draft fan on the dust removing device should be started first, and then the dust removing motor should be started; if the production needs to be interrupted, the stop button of the dust removing motor should be pressed first, and then the induced draft fan work should be stopped. (2) Clean the dust in the cyclone vacuum cleaner regularly to avoid excessive accumulation and affect the dust removal effect. (3) After starting the dust removal device, the working condition of the induced draft fan should be checked frequently. (4) The dust removal electrode should be maintained on schedule to ensure normal operation. (5) When carrying out anti-corrosion production, the surface of the steel pipe should be checked at least once an hour for microdust treatment.
Fourth: steel pipe preheating (1) after the microdust treatment of steel pipe, before epoxy powder coating, should be preheating treatment, using KGPS-750uw constant power medium frequency machine to the steel pipe for heating, the preheating temperature must be in line with the temperature required by the epoxy powder coating, but the maximum shall not exceed 275 ℃. (2) Check the water level of the medium frequency circulating water pool, make sure the water volume is at least 2.5~3 cubic meters. Start the medium-frequency circulating water pump, check whether all the circulating water pipes are leaking or not, and start the medium-frequency device machine only when you are sure that everything is normal in the circulating water pipes. (3) According to different pipe diameter steel pipe feeding speed and predetermined heating temperature, using the experimental tube on the operating line to adjust to determine the production is the output power value of medium frequency heating. (4) The use of advanced temperature measuring instruments to measure the temperature of the steel pipe preheating, improve the accuracy of the measurement to ensure that the steel pipe for powder coating, the steel pipe preheating temperature in the range recommended by the powder coating manufacturer. (5) For anti-corrosion production, measure and record at least once an hour to determine the preheating temperature of the steel pipe when powder coating.
Fifth: epoxy powder roll coating or spraying due to the thermal roll coating and thermal spraying process differences, not described in detail here. (1) The adhesive coating must be carried out in the epoxy powder gelatinization process. (2) When the lateral winding process is used, it should be ensured that the polyethylene (polypropylene) in the lap part and the polyethylene (polypropylene) on both sides of the weld seam are completely rolled and compacted, and the surface of the polyethylene (polypropylene) layer should be prevented from being crushed.
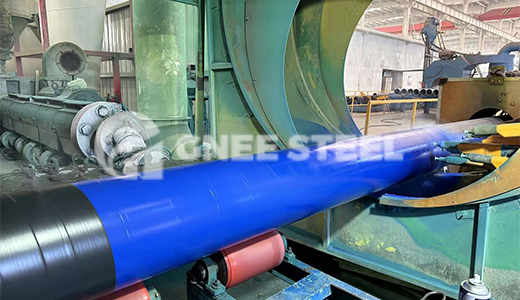
Sixth: circulating water cooling steel pipe anticorrosive layer production is over, should be promptly cooled and fixed molding, can be used to circulating water pouring coating room for anticorrosive steel pipe anticorrosive layer surface layer of the cooling, cooling to take a section by section sub-methods. (1) Before production, start the circulating water pump motor of the coating room. (2) Adjust the valve switch of the cooling water pipe to control the size of the cooling water to avoid the impact on the anticorrosive coating caused by the excessive speed of the water flow, which affects the appearance and molding quality of the coating. (3) In the steel pipe into the pouring coating room before the first set of drive wheels, the first cooling water for cooling. So that the steel pipe surface layer just anticorrosion on the coating in rolling to the first group of rubber wheels, the anticorrosion layer will not be damaged and remain intact. (4) According to the size of the pipe diameter and the difference in ambient temperature, take 2~4 sections of cooling water for cooling by section by section, the cooling temperature of the steel pipe is not higher than 60 ℃, and to ensure that the fusion bonded epoxy coating is fully cured. (5) The appearance of the coating shall be smooth, uniform in color, free of bubbles, cracks and shrinkage holes, mild orange peel pattern is allowed, and the thickness of the coating shall meet the design requirements. (6) At least the thickness of the anticorrosion layer of the 1st, 5th and 10th steel pipes shall be checked for each consecutive production lot, and at least one of every 10 shall be sampled thereafter. (7) If the customer has requirements, it shall be implemented according to the customer's requirements.
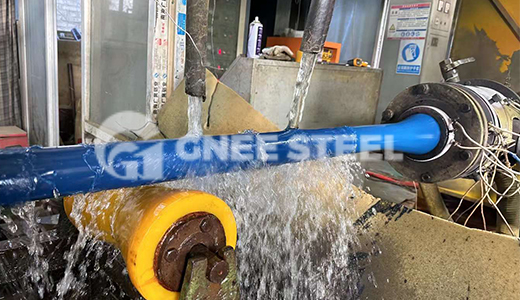
Seventh: cutting stay head steel pipe after cooling water cooling of the anti-corrosion layer, according to the provisions of the pipe end of the reserved length of 100-120mm requirements.
Eighth: trimming pipe end stay head (1) polyethylene (polypropylene) layer end face should be formed not more than 30 degrees of chamfer, polyethylene (polypropylene) layer can be retained outside the end of the epoxy powder coating of not more than 20mm. The end of the anti-corrosion pipe should be prevented from peeling or buckling of the anti-corrosion layer. (2) Pipe end retaining head using electric wire brush for pipe end retaining head treatment, operation by 2~3 times in sections to meet the standard requirements. (3) used to grind the end of the pipe to leave the head of the anticorrosion layer chamfering steel wire brush, the work surface should be flat, no bumps and dents.