Spiral submerged arc welded steel pipe in the application of spiral submerged arc welded steel pipe structure for welding and cutting is inevitable.
Because of the characteristics of the spiral submerged arc welded steel pipe itself, compared with plain carbon steel spiral submerged arc welded steel pipe welding and cutting has its own particularity, more likely to produce a variety of defects in its welded joints and heat affected zone (HAZ), spiral submerged arc welded steel pipe welding function is mainly manifested in the following aspects, high temperature cracking in the high-temperature cracking referred to here refers to the cracks related to welding.
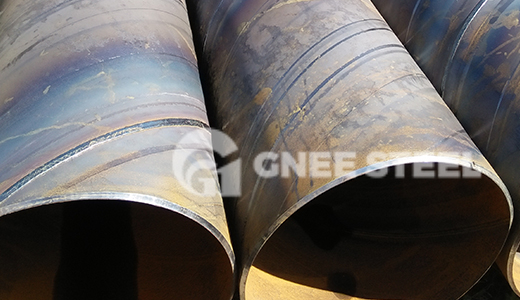
High temperature cracks can be broadly divided into solidification cracks, micro cracks, cracks in the HAZ (heat affected zone) and reheating cracks.
Low temperature cracking sometimes occurs in spiral seam submerged arc welded steel pipe. Because the main reason for its generation is hydrogen diffusion, the degree of restraint of the welded joint and the hardened organization, so the solution is mainly to reduce the diffusion of hydrogen in the welding process, appropriate preheating and post-weld heat treatment and reduce the degree of restraint.
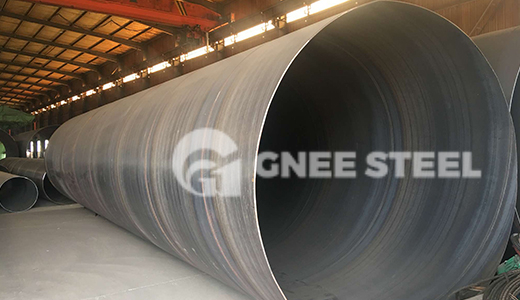
In the spiral seam submerged arc welded steel pipe welding, welded joints in the area of the austenite amount decreases and has an impact on the toughness. In addition, following the increase of ferrite in it, its toughness value has a significant tendency to decrease. It has been proved that the high purity ferritic stainless steel welded joint toughness decreased significantly because of the mixing of carbon, nitrogen, oxygen.
Some of these steel welded joints in the oxygen content increases after the birth of oxide inclusions, these inclusions become the source of cracks or crack propagation pathway makes the toughness decline.